The Internet of Things (IoT) promises to enable many new business models. In industrial markets, the concepts of IoT, or Industrial IoT (IIoT), are already gaining traction. At the simplest level, for example, IIoT provides the ability to more closely monitor a production line in near real time, or manage buildings and their associated plants more efficiently. IIoT also offers the ability to radically change your whole business approach.
While it is easy to grasp the basic concepts behind any IIoT implementation, if you dig a little deeper there are a significant number of decisions to make in the way it will operate. For example, a cloud platform might well be able to establish trend lines on how often a motor is switched on/off to activate a conveyor belt, but does it need to rely on the cloud platform to tell it when to turn on or off?
With IoT, one of the core principles is that data from a myriad of sensors (that could be on a construction vehicle, a production line or an elevator) is sent to the cloud.
For example, the data coming from a vibration sensor on an excavator’s main hydraulic pump might begin to exhibit mechanical vibrations greater than a pre-defined safety level. Caught early this can be inspected and a faulty or worn part replaced during a preventive maintenance cycle. Failure to respond to this is likely to cause the excavator’s operation to become unsafe, or fail completely, or in the case of an industrial robot’s actuator, to jam, stopping the whole production line. IIoT analysis and monitoring routines can pick up these potential failures up and alert management to the need for maintenance. The control aspects of this cloud computing approach provide the overall operational management of the factory, plant or building, along with the individual assets used in order to maintain the highest levels of production or operational efficiency. In principle, cloud computing seems ideally matched to deliver the requirements of a smart factory approach. However, get into the detail and there are a number of challenges to this approach.
Industry 4.0 clearly identifies these, the most critical being increased security issues, very short and stable latency times, maintaining the integrity of production processes and accommodating decentralized decisions. Needless to say that any mention of a cloud-based approach also assumes 100% availability of fast and resilient broadband service with fall-over protection. Linking every aspect of a manufacturing facility, building or heavy plant clearly will benefit from the management data that can be extracted and analysed from it. Trends, improvements and impending maintenance concerns are core data but from the control perspective using a cloud-based application introduces too much latency, most of which is dynamic.
A successful Industry 4.0 / smart factory implementation needs all the benefits that a cloud computing approach yields but to address the security, latency, bandwidth and legacy infrastructure concerns highlighted above.
This whitepaper, by IoT Solutions company relayr, will illustrate the concepts between IIoT and dependence on a cloud-based computing approach. Taking this a stage further, the paper will introduce the concepts behind adopting a fog computing approach where a cloud platform delegates some aspects of control to local infrastructure elements.
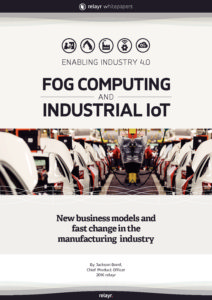