Despite the well-documented advantages of digital transformation and smart factories, it can be overwhelming to know where to begin.
Cultivating a green patch in your brownfield can be a good way to start. A green patch is bigger than a pilot project, because it is a full-scale production system, but it is a small investment than a greenfield. Typically, the project scope would be one line or cell.
We talked with John Kowal, Director of Business Development at B&R Industrial Automation, a global supplier of advanced machine control solutions, about adaptive machines and how to cultivate a green patch within a brownfield.
Questions answered:
- What are the benefits to manufacturers of transitioning to IIoT/connected factories?
- Do manufacturers have to rip and replace existing equipment in order to make this transition or can they retrofit existing equipment?
- What are some challenges manufacturers with legacy equipment face when trying to transition to manufacturing IIoT or smart factories?
- Tell us about the concept of a ‘green patch’?
- Where is the ideal environment to implement a green patch?
- What are some supporting factors within the company you need to get a green patch project in place?
- What data/knowledge will manufacturers take from this green patch project that will help guide future decision-making?
- How do you measure the success of a green patch project?
- What is the next step after a successful green patch project? How do manufacturers roll this out across their whole facility?
Click through to read the complete interview.
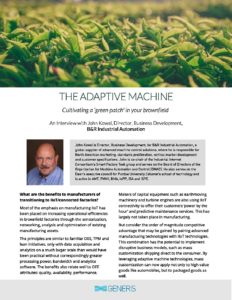