The Austin Company offers a comprehensive portfolio of in-house services, including planning, architectural design, engineering, design-build, construction management, and construction, as well as site location and operations improvement consulting, for commercial and industrial companies throughout North America, Europe, and Asia.
In advance of the American Manufacturing Summit, we asked them to highlight some of their favorite manufacturing facilities they have worked on across different industries, from bakery production to heavy industrial manufacturing.
1. Airbus Aircraft Manufacturing Center – Mobile, AL – 423, 600 SF
The Austin Company provided design, engineering, and construction administration services for the most critical components of the overall project – the Final Assembly Line, Logistics Building, and Service Building at the new manufacturing center.
In response to the project’s aggressive schedule, expedited design of the pilings and pile caps allowed this construction work to begin just six weeks after award of the design. Austin’s precise engineering resulted in the completion of all design and engineering work for completed construction documents in just five months following the contract award.
Special design considerations were necessary for these buildings due to the location and local soil and weather conditions, involving flood protection, heavy rain, corrosive protection, deep foundations and influence of hurricanes, including gale-force winds up to 135 MPH.
2. Bimbo Bakeries USA | Lehigh Orograin Bakery – Lehigh Valley, PA – 230, 610 SF
Bimbo Bakeries USA (BBU) implemented a strategy to develop new and more automated and efficient bakeries with upgraded food quality standards and increased production capacity. This strategy drove the demand for BBU’s bakery facility in Lehigh County, Pennsylvania. The Austin Company has successfully completed multiple bakery projects for BBU and was once again called on to deliver design-build services for this new facility.
Situated on 29 acres, the facility includes bakery; packaging and warehouse areas; a basket wash area; entry, office and mechanical areas; and other support. The new facility features multiple production lines and utilizes some of the fastest baking equipment available.
To support Bimbo’s vision for environmental sustainability, the facility was designed and constructed to achieve LEEDⓇ standards and was awarded LEEDⓇ Gold Certification.
3) Colgate Palm-Olive Toothpaste Manufacturing Facility – Morristown, TN – 250,000SF
Colgate-Palmolive, the global leader in oral care, solicited the Austin Company to build a state-of-the-art 250,000 SF dental cream facility in Morristown, Tennessee. The manufacturing facility, employing more than 220 people, was designed and built according to Colgate’s rigorous global standards and in accordance with FDA regulatory requirements.
Austin Consulting, the site selection consulting branch of The Austin Company, initially assisted in locating the Morristown site, and provided a full range of site location and incentive negotiation services. Once the site was selected, Austin continued to provide architecture, engineering and construction services to deliver a world-class facility on an accelerated 10-month design and construction schedule.
This project achieved LEEDⓇ Silver Certification.
4) Mitsubishi Power Systems America Heavy Industrial Manufacturing Facility – Pooler, GA – 440,000 SF
This heavy industrial facility is Mitsubishi Power Systems America’s latest expansion effort in Savannah and serves as the company’s next step in providing world-class power generation services and products for the gas and steam market. The Austin Company provided architectural design, interior design, and engineering services, while their sister company Batson-Cook provided construction services.
The design-build project consisted of more than 440,000 SF and was completed in phases. The 20,000 SF Balance Bunker Turbine Balancing Test Facility was the most complex of all the projects. Austin’s design and precise engineering work included an 8,000 horsepower electric motor to turn the rotors during balancing. In addition, 6-foot thick Bunker walls were designed to protect the surrounding area from rotor elements that may come loose during testing. The walls were also heavily reinforced inside and out with rebar and steel plates.
5) Northrop Grumman Aerospace Systems Aircraft Integration Center of Excellence Building 100 – St. Augustine, FL – 366, 000 SF
In St. Augustine, Austin worked on the expansion of Northrop Grumman’s Aircraft Integration Center of Excellence – the production home of the U.S. Navy’s E-2D Advanced Hawkeye. The new 366,000 SF aircraft manufacturing facility, known as Building 100, is located on an existing Northrop Grumman site and will support production of the E-2D Advanced Hawkeye Aircraft. The new facility replaces a smaller building, Building 7 – the former E-2D assembly building, which was demolished to make room for Building 100.
Phased project construction was necessary due to site limitations. The existing site included a parking lot and multiple buildings, all of which were demolished for Building 100 construction. In addition, considerable site work to reroute underground utilities and drainage was required.
Building 100 was designed, engineered and constructed with LEEDⓇ features and performance characteristics and was awarded LEEDⓇ Gold Certification.
Click through the different case studies below to learn more about The Austin Company’s work.
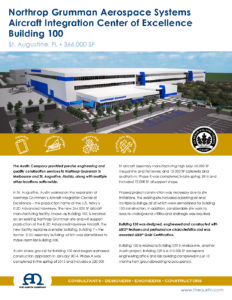
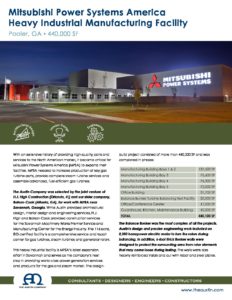
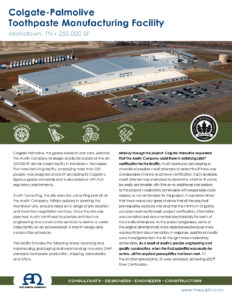
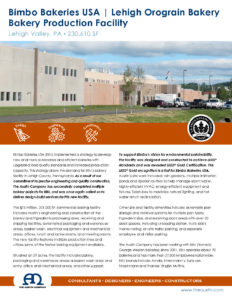
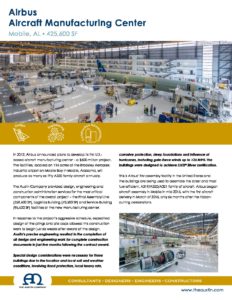