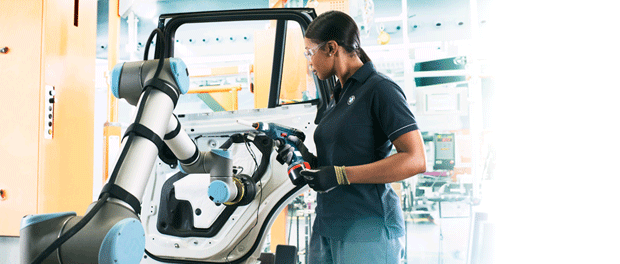
BMW uses Universal Robots’ Co-bots which can work safely alongside humans, and also use innovations in ergonomics to make work safer for their employees.
The promise of Industry 4.0 is being realized in the automotive industry, and BMW is at the forefront of the evolution of automated production. At last year’s American Manufacturing Summit, Dirk Hilgenberg, VP, Assembly at BMW shared with us how BMW is incorporating Industry 4.0 concepts to innovate at each stage of the production process, from design to post-market.
Design
Hilgenberg says 3D printing has become a commodity for BMW, something he couldn’t have believed he would be saying three years ago. They are now producing over 25,000 prototype parts per year; as a result, the hardware design phase has accelerated and entire development loops have changed completely. 3D printing is also being used for spare parts. Now, rather than having spare parts built and lying somewhere, which is an investment in assets, BMW can create them on demand.
Planning
In the planning phase, BMW has had their facilities 3D scanned and digitized their entire assembly shop to create a 3D accurate model they can play with to test and plan various configurations of product lines, equipment, processes, and people.
Launch
Similarly, to reduce time to market, BMW is using digitalization and virtual commissioning. They can virtualize/digitalize a product to test it, and cut down on physical build phases. Hilgenberg says they can simulate a lot with structural parts, but it’s much more difficult with parts like rubber, or scenarios where they have to simulate gravity. As such, they do have mixed reality worlds, which incorporate some hardware and some digital components.
Implementation
BMW is involved in a number of educational collaborations to strengthen their innovation and workforce pipeline.As a founding partner of Clemson University’s International Center for Automotive Research, BMW is part of an automotive ecosystem where industry and academia meet to conduct research on lightweight design, component production, quality, sustainability, safety and much more. Cooperation with Georgia Tech provides input for BMW’s production and assembly locations worldwide. The collaboration leverages mutual strengths in industrial engineering and production systems in preparation for increasing global digitalization.
Series Production
At the series production phase, BMW is utilizing automation, but also innovating in how to make work better for their employees. The division of labor in their facilities gives robots domain over repetitive and physically demanding tasks, while humans work on things that require finesse and craftsmanship. Combining the strengths of both, they can create a safe and ergonomic work environment, where technology supports and assists associates in a whole new way. They utilize cobots, which can work safely alongside humans, and also use innovations in ergonomics, such as exoskeletons that support the arms of people who have to do work overhead.
Data & Analytics
BMW is taking advantage of the low cost of sensors and installing them to monitor brownfields, drives, conveyor belts, and bearings. Making use of the “data lake”, they are able to predict when there will be a problem and schedule maintenance accordingly.
To learn where to begin your own digital transformation, check out the Smart Factory Transformation Checklist.